In the heart of Rajasthan’s Marwar region lies Jodhpur, a city renowned for its flourishing stainless steel industry. This industry, however, is sustained by the unyielding labor of thousands of migrant workers, predominantly from Bihar and Uttar Pradesh. These individuals come to Jodhpur seeking stable employment and a better future for their families. Yet, the reality they encounter starkly contrasts with their aspirations. Instead of opportunity and security, they face hazardous working conditions, exploitative labor practices, and a disregard for basic rights. The question thus arises: is the economic growth of this industry worth the steep human cost it exacts?
Migration to Jodhpur has long been a beacon of hope for workers from Bihar, a state plagued by high unemployment rates and limited economic opportunities. For many, the move signifies the promise of financial stability and improved living standards. Yet, these dreams are often shattered upon arrival. Instead of steady jobs with living wages, migrants are met with overcrowded accommodations, grueling work hours, and unsafe work environments.
The allure of finding work 1500 km away quickly fades as workers confront the harsh realities of production-driven environments.
The allure of finding work 1500 km away quickly fades as workers confront the harsh realities of production-driven environments. Factories prioritise profits over people, with minimal investment in safety protocols or employee welfare. The transformation of hope into disillusionment is both rapid and distressing.
The overbearing pressure of production on workers
Jodhpur’s stainless steel industry thrives on relentless competition, where maintaining profit margins necessitates ever-increasing productivity. The production process is grueling. Factories churn out hundreds of tons of steel products daily, from utensils to industrial components. Workers, often with no mechanised support, are required to manually handle large sheets of steel—lifting, bending, and cutting them into shape. This labor-intensive process takes a severe toll on their physical health, with constant exposure to sharp edges and heavy materials.
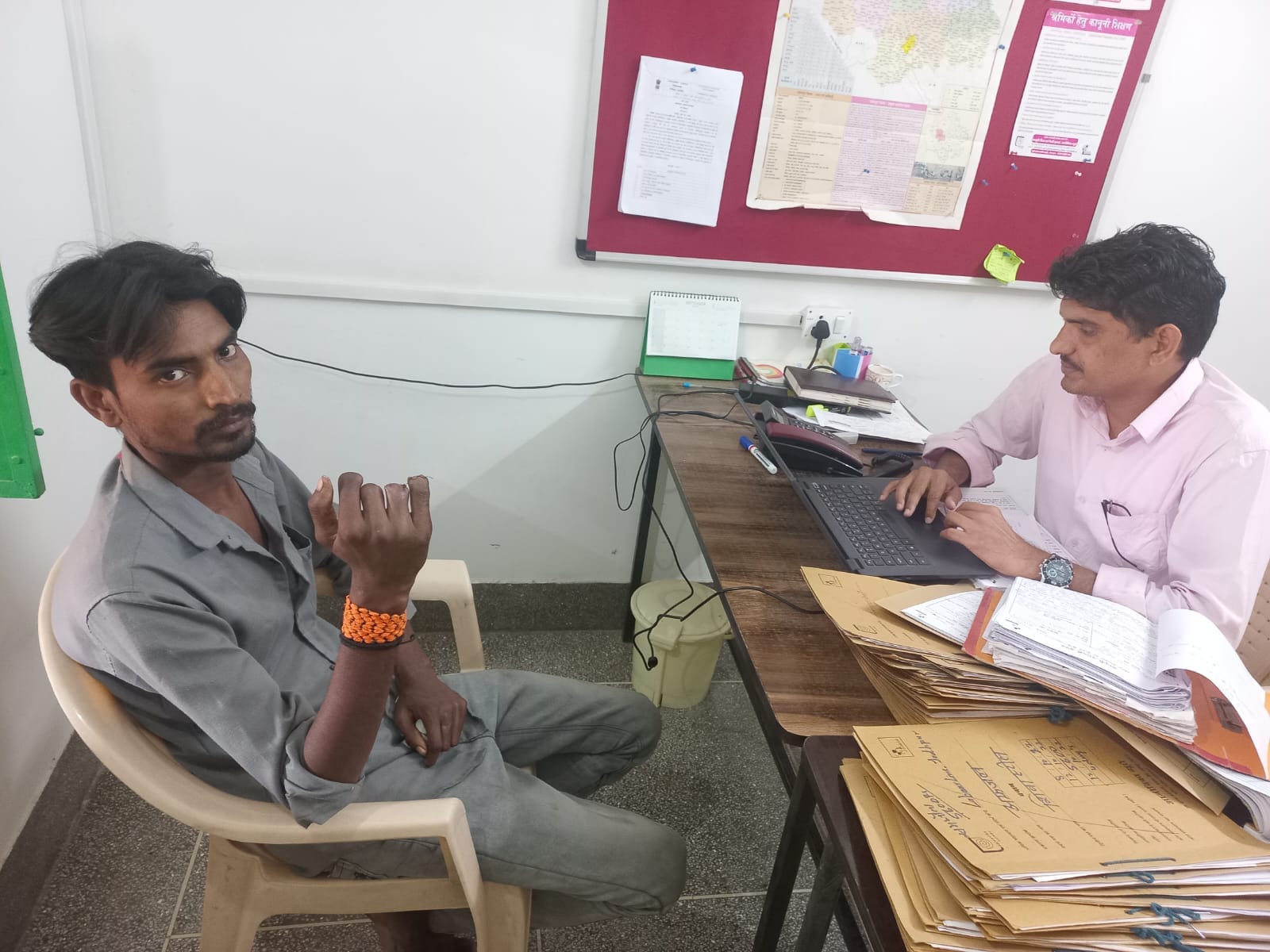
The contractors (thekedars) overseeing these workers enforce strict timelines to meet production targets, ensuring that the workflow never slows. Twelve-hour shifts sometimes stretching even longer are the norm. Exhaustion becomes a permanent state, leading to frequent mistakes, which, in a workplace brimming with unguarded machinery, often result in serious injuries.
Despite these conditions, a frivolous mindset prevails among factory owners and contractors. Safety lapses are dismissed, injuries are trivialised, and workers are pushed to their limits in the name of efficiency. The mantra is clear: production must not stop, no matter the human cost.
Occupational health hazard for workers: blood on the steel
The gleaming stainless steel utensils that grace our dining tables often carry a story of blood, sweat, and tears—a story seldom told. Behind the polished surface lies the grim reality of workers in Jodhpur’s stainless steel industry, a sector where the pursuit of profits outweighs the safety and well-being of those who power it.
Every cut of steel seems to cut deeper into the lives of the laborers, many of whom bear permanent marks of their toil. The types of injuries sustained in these industries are harrowing and diverse. Workers frequently suffer loss of fingers and limbs, a common and devastating outcome of being caught in unguarded machinery or handling sharp metal sheets without adequate protective gloves. In many cases, these accidents result in lifelong disabilities, robbing workers of their livelihoods and independence.
In many cases, these accidents result in lifelong disabilities, robbing workers of their livelihoods and independence.
Burn injuries are another cruel reality. Many workers come into contact with hot objects, sparks, or molten materials during steel processing. Without proper gear such as heat-resistant gloves or face shields, they are left vulnerable to severe burns. For some, even a single moment of exposure can lead to disfigurement, pain, and in the worst cases, death.
A workplace without safety: breathing hazards, bearing risks
The absence of basic safety measures exacerbates the risks. Workers inhale harmful fumes and fine metal particles, leading to respiratory issues and long-term health problems. The lack of masks and proper ventilation creates an environment where each breath is a hazard.
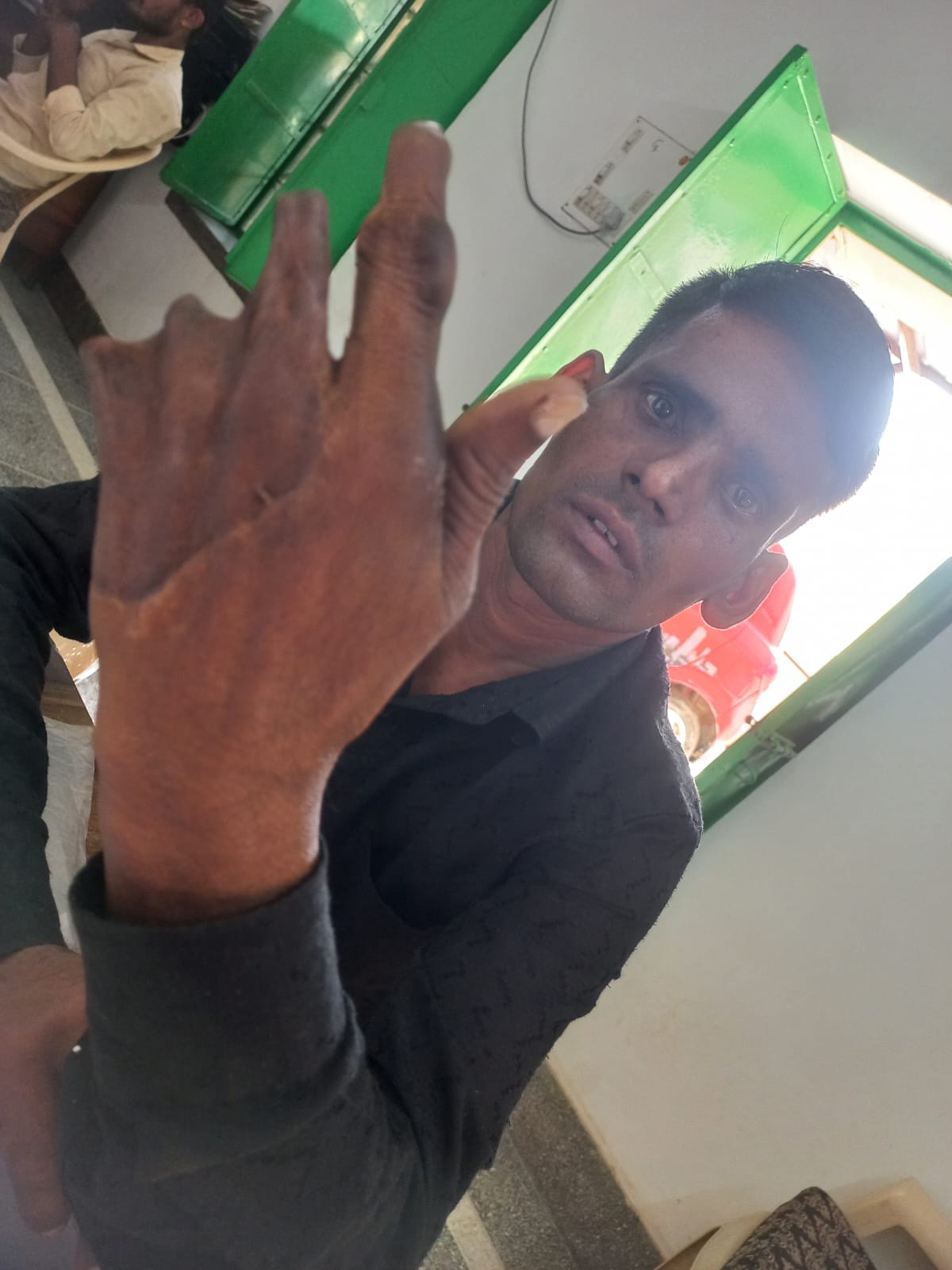
Many suffer back and neck injuries from lifting heavy loads, often without proper training or equipment. Broken bones, head trauma, and fractures are disturbingly common, especially in incidents involving machinery malfunction or the collapse of structures. In the chaos of unregulated workshops, every workday is a gamble.
Yet, the most tragic aspect is the indifference of the system. Factory owners often dismiss these injuries as mere “accidents” caused by worker negligence, evading their legal and moral responsibility. For workers, these injuries mean more than physical pain—they signify the slow erosion of hope and dignity.
What needs to be done?
To safeguard Jodhpur’s steel workers, urgent measures must be implemented. The prevailing mindset of employers needs to change. Employers must recognise that investing in worker safety and health is not just a moral obligation but also a long-term strategy for sustained productivity. Ignoring safety today only leads to higher turnover, legal liabilities, and diminished output in the future.
Proper personal protective equipment (PPE) such as gloves, masks, and face shields must be provided on a timely basis
Proper personal protective equipment (PPE) such as gloves, masks, and face shields must be provided on a timely basis. Many workers complain that due to the intense manual labor, their gloves wear out quickly. Gloves should ideally be replaced daily, yet contractors supply them only once every four days, leaving workers vulnerable. This inconsistency must be addressed with weekly or even daily replenishments of safety gear.
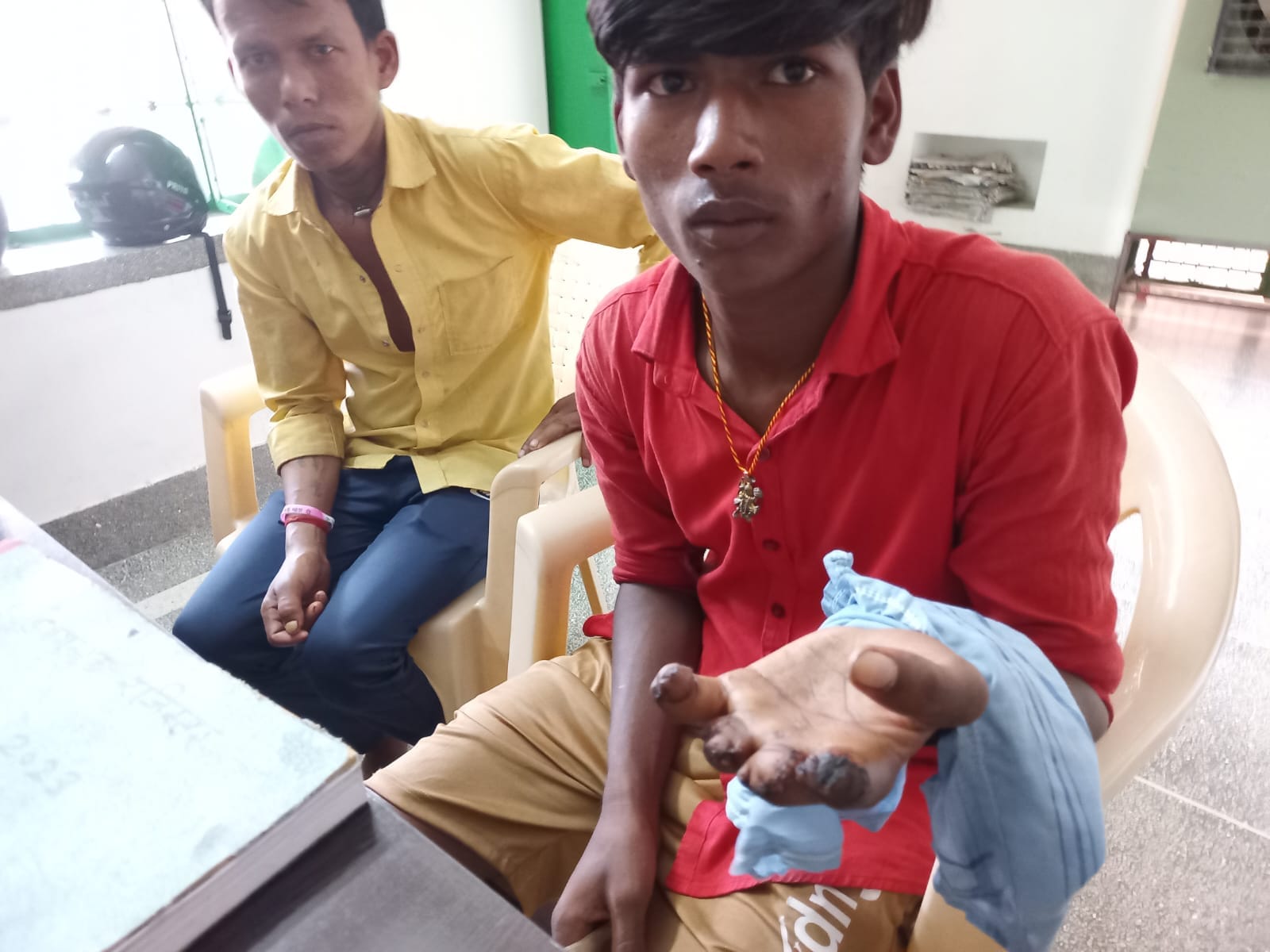
Regular factory audits and inspections are critical to ensure compliance with occupational safety standards. Employers must also be penalised for safety violations, incentivising them to maintain a secure workplace. Additionally, on-site medical facilities and guaranteed compensation for injuries can provide workers with the support they need in case of accidents.
Encouraging unionisation and worker organisations can empower laborers to advocate for their rights. Awareness campaigns on occupational safety and labor rights should be conducted by the government to educate workers about the importance of demanding better conditions.
Responsible citizenship: rethinking steel consumption
As consumers, we also bear a share of the responsibility. Just as many of us avoid products tested on animals or choose sustainably sourced goods, we must question the ethics of the steel products we purchase. Factories that exploit labor and neglect safety should not be allowed to profit unchecked. A certification system, akin to a hallmark, could be introduced to signify ethically produced steel products. Such a system would encourage factories to adopt safer and more humane practices.
Consumers can also push for greater transparency by supporting audits and initiatives that monitor factory conditions.
Consumers can also push for greater transparency by supporting audits and initiatives that monitor factory conditions. The next time you buy a stainless steel utensil, think beyond its shine. Ask questions about where and how it was made. Let your choices reflect the value you place on human dignity and fair labor practices.
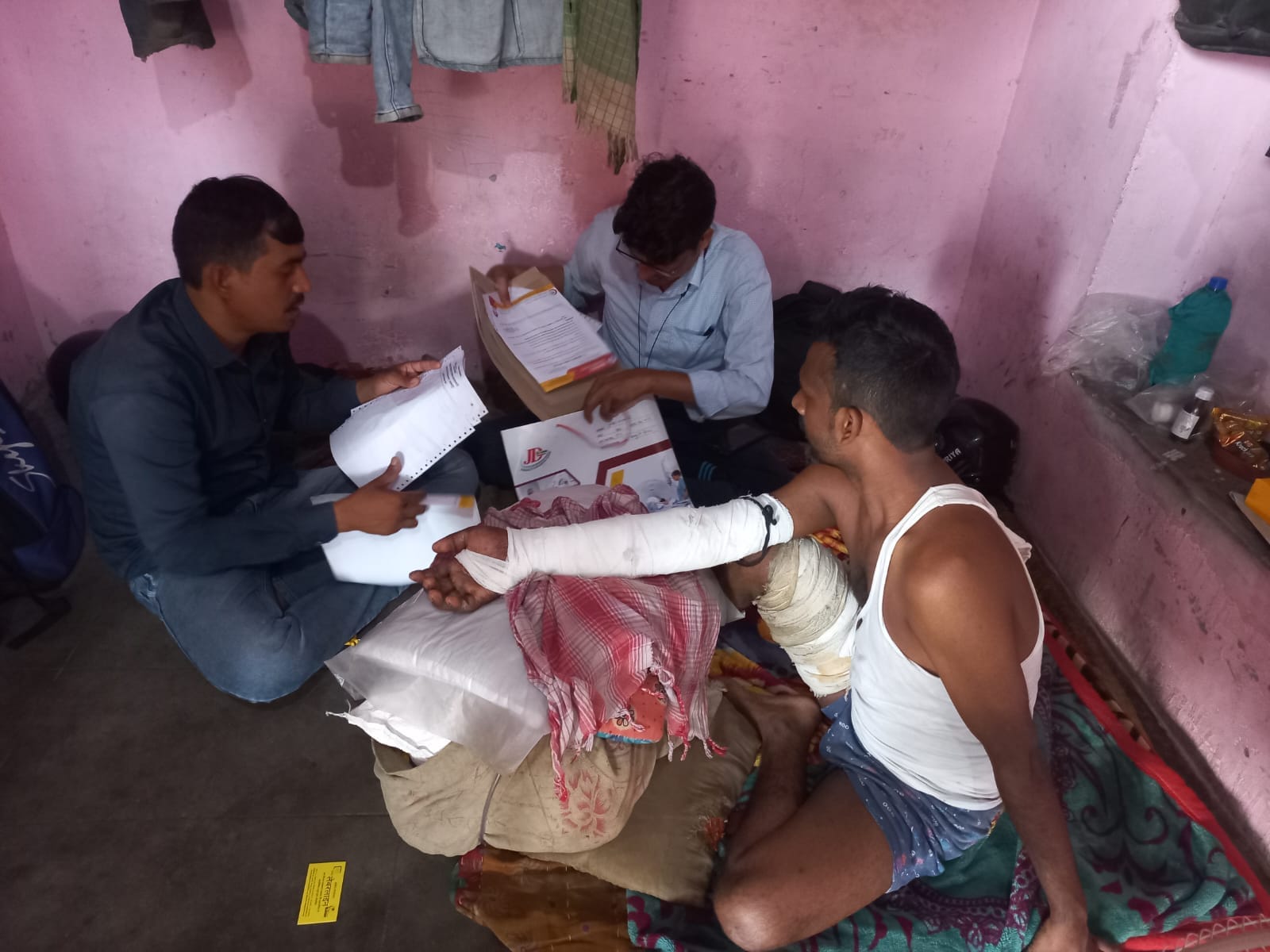
How many meals will we consume on blood-soaked utensils before recognising the cost? Every polished plate reflects a worker’s unacknowledged sacrifice. The next time you hold a shiny stainless steel spoon or plate, remember the cost paid by those who crafted it. Their blood has seeped into the steel, and their pain is etched into its polish. The question remains: how much longer will we let this invisible sacrifice go unnoticed?
This article was written while working as an India Fellow at Aajeevika Bureau, where the author engaged in conversations with steelworkers in Jodhpur about occupational safety, hazard, and their overall health.
About the author(s)
Sahil is an India Fellow working with Aajeevika Bureau, where he focuses on promoting labor rights and raising awareness among migrant workers. His work includes conducting sessions on occupational safety, workplace rights, and the importance of collectivization. He also facilitates discussions on issues such as wage stagnation, workplace hazards, and legal redressal mechanisms, empowering workers to advocate for their rights and improve their working conditions.